Zinc Plating vs Powder Coating for Corrosion Resistance – SendCutSend
Powder coating and zinc plating are two popular methods for protecting steel from corrosion. Both are used in laser cutting applications and offer advantages over one another. Though both methods have their benefits, it’s important to know how each works so you can choose the best option for your project.
What is Zinc Plating?
Zinc plating is also known as zinc electroplating, or zinc electrodeposition. It refers to a process in which electricity is used to deposit a thin layer of one material onto another. For what we’re discussing today, it would be a thin layer of zinc deposited onto a steel part.
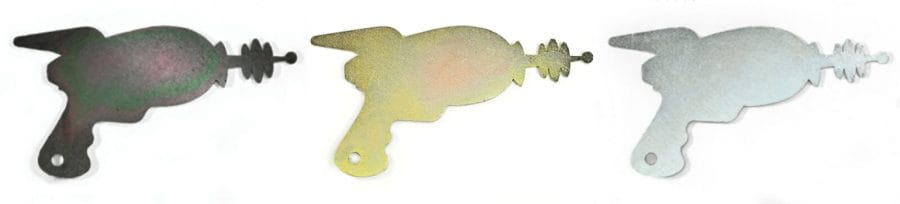
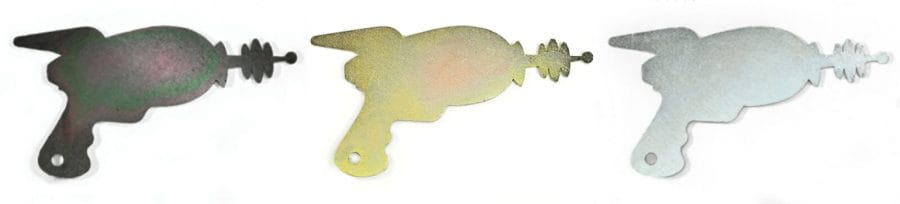
If you’re interested in a slightly more detailed explanation, read on. The process starts by submerging a piece of zinc (known as the anode) and the steel part to be plated (known as the cathode) into a zinc ion solution (zinc dissolved in a liquid with a small electric charge). Then a positive charge is applied to the zinc anode and a negative charge is applied to the steel cathode. Small amounts of the zinc anode will dissolve and be attracted to the negatively charged steel. These zinc ions move through the solution and build up a thin layer over the surface of the steel. The thickness of the layer can be controlled through several factors, such as the level of charge, time spent, make up of the solution, etc.
Chromate Conversion
It’s very common after a part is zinc plated to also perform a chromate conversion process. The purpose of a chromate conversion is to strengthen the outer zinc layer. The process involves submerging the zinc plated part into a bath of chromates, salts and acid typically. In just a few seconds, the outermost skin of the zinc reacts with the bath and turns leaving a stronger shell on the zinc.
What is Powder Coating?
The aptly named powder coating process involves coating a material (again, steel in our case here) with a very fine dry powder and then heating the part to the point of melting the powder into a hard shell.
In a little more detail, the powder itself is typically made up of different materials including specific polymers and resins along with a handful of additives to get the product to behave in the desired way. These are all mixed together and then ground into a very fine powder. To get the powder to stick to the steel part, electrostatic deposition is used. That’s where the powder is given a small electric charge and the part being coated is grounded. As the powder is gently blown over the part, the charged powder will stick to the part. This is similar to how rubbing a balloon on your hair makes it attracted to the balloon because they have a small opposite charge.
Once the part is covered in dry powder, the part is immediately moved into an oven and heated until the powder melts together. The part is then allowed to cool and you have a steel part covered in a hard polymer shell.
Pros and Cons
When it comes to protecting steel parts from corrosion all methods have their advantages and disadvantages. Before we look at our two methods, let’s look at why steel corrodes in the first place.
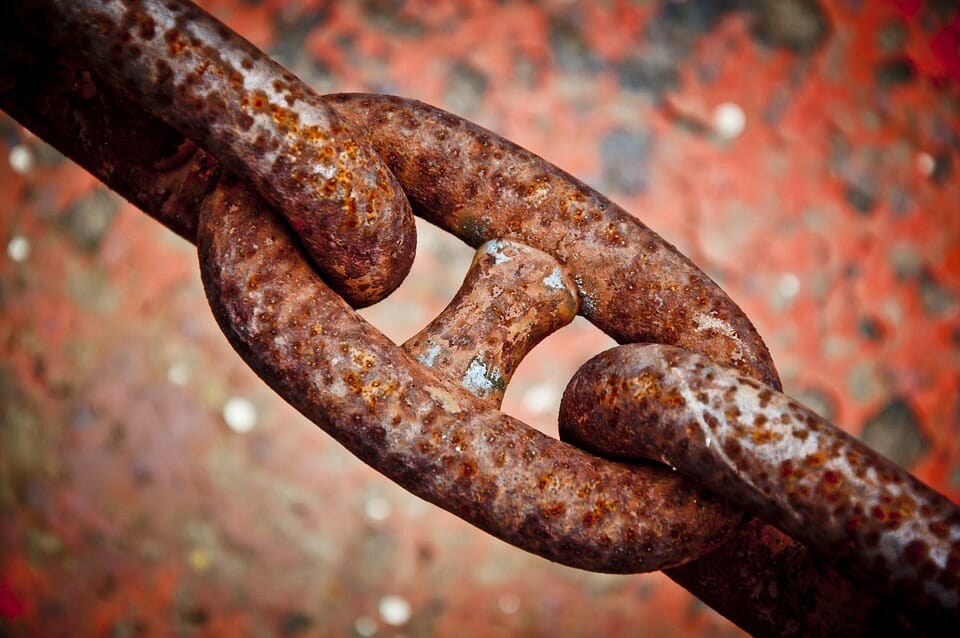
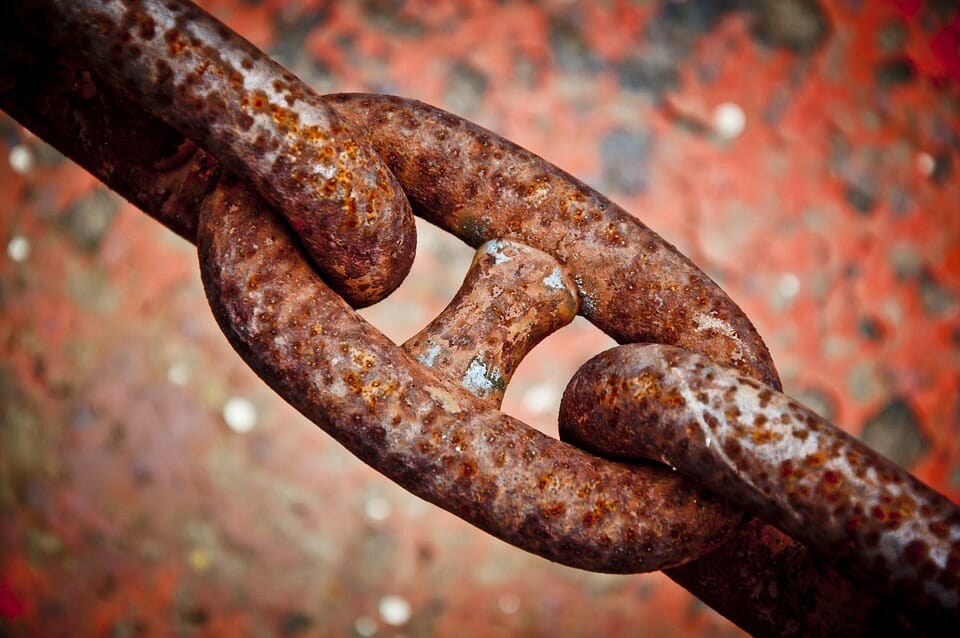
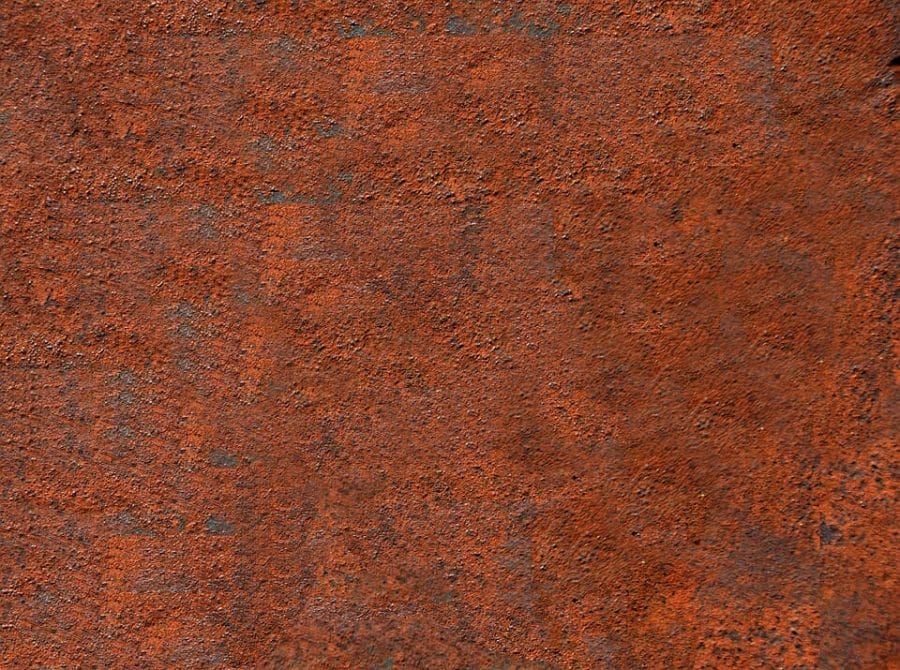
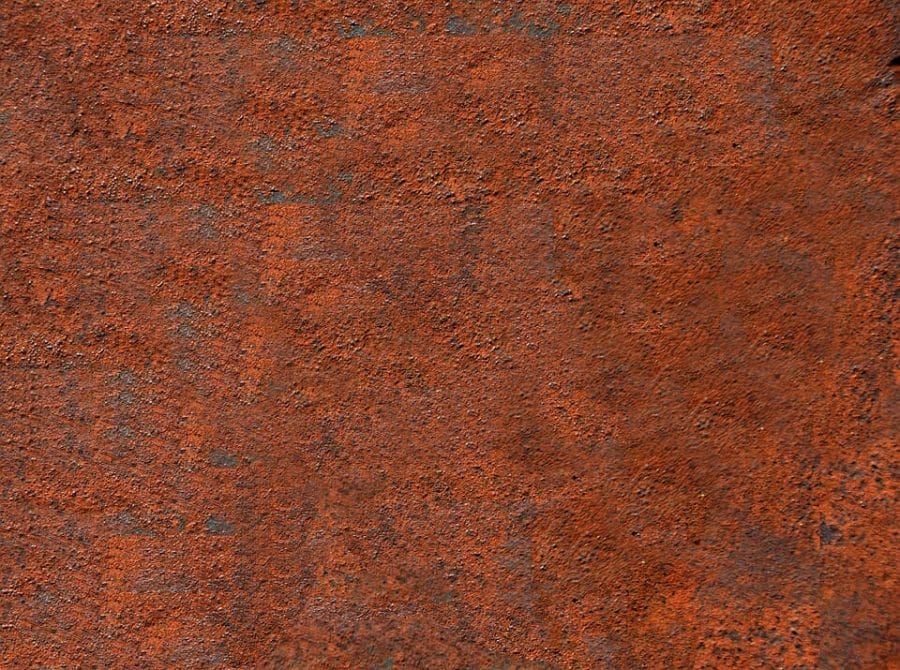
What we refer to as corrosion on steel is commonly known as rust, or iron oxide. There are other kinds of corrosion, but we’re going to focus on rust here. Rust/iron oxide forms when the iron in steel (steel is more than 95% iron) reacts with oxygen. Unfortunately iron oxide is a weaker material than steel and will easily break away from the base material. There’s oxygen in the air, so exposed steel parts that are exposed to air will almost certainly rust over time. There are a lot of factors that can affect the rate at which steel rusts. Humidity for example can greatly speed up the process. Salts also have a huge influence on corrosion rates. So steel parts anywhere near the ocean are likely to rust extremely fast.
Let’s get into the pros and cons of zinc plating and powder coating when trying to prevent corrosion.
Pros of Zinc Plating for Corrosion Resistance
One of the biggest advantages for zinc plating when it comes to corrosion resistance is that it can help prevent corrosion in two ways. The first is to form a barrier between the steel and oxygen. If the oxygen can’t get to the steel, it can’t react. This is true of most methods for preventing corrosion.
The second way zinc plating helps prevent corrosion is more interesting. Zinc can prevent rust on steel just by being close to it. Zinc will more readily react with the oxygen and use up those oxygen molecules before they reach the steel. This means that even if the zinc plating layer is damaged and the steel is exposed, the zinc is still providing some level of protection against rust.
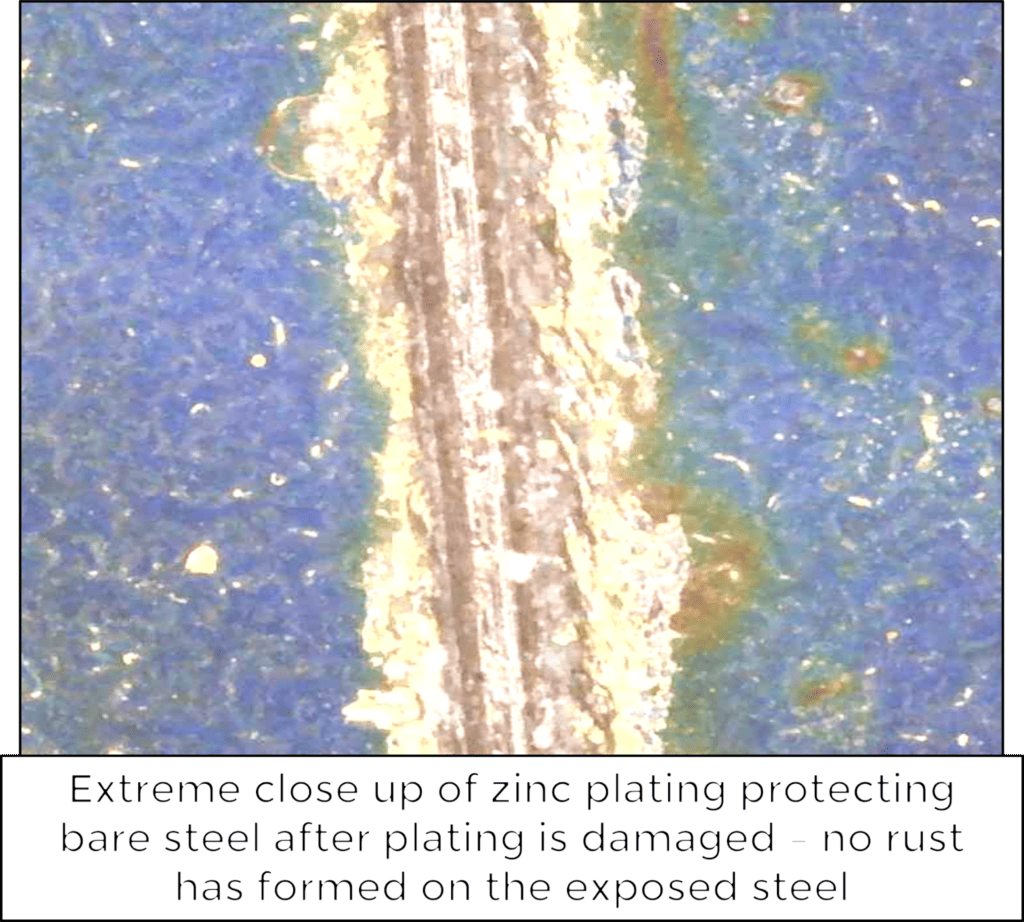
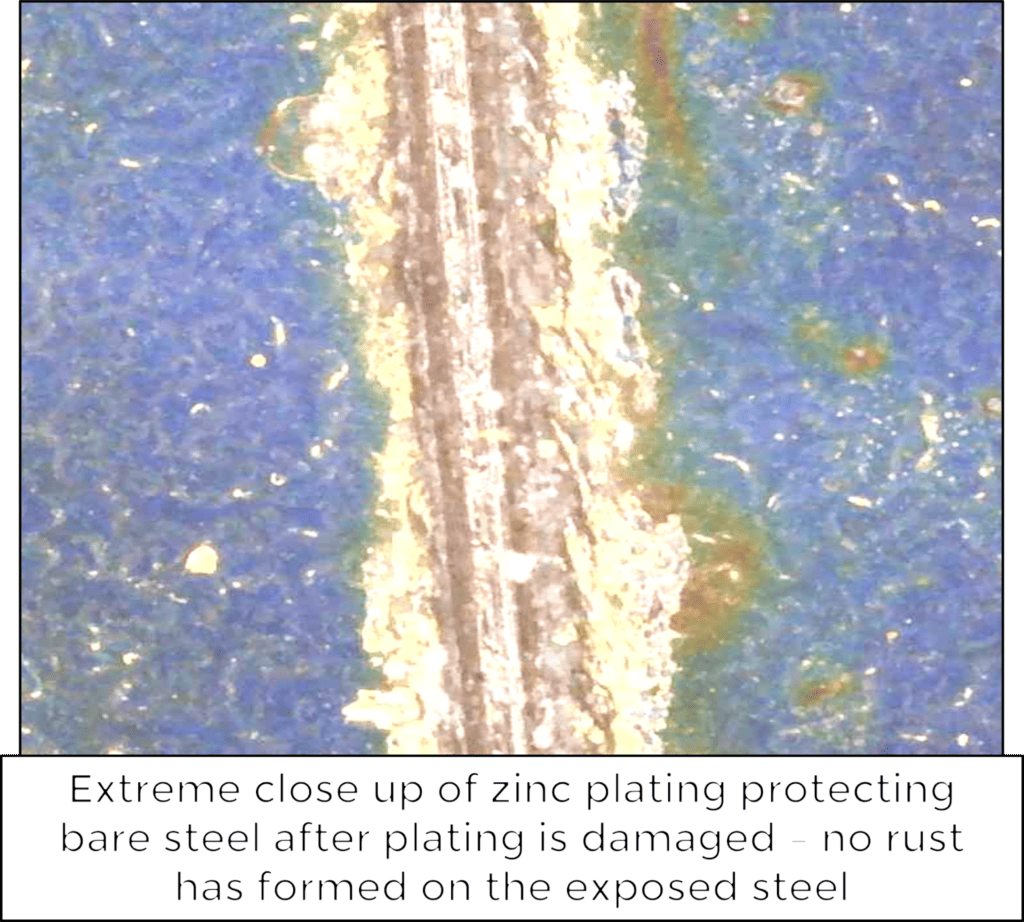
Zinc plating also has a slight advantage in adhesion. Due to the electrodeposition process, the zinc is attached to the steel substrate extremely well. It’s much less likely to chip and break away.
Cons of Zinc Plating for Corrosion Resistance
Zinc plating also has some disadvantages when it comes to protecting your parts. It’s not as durable as a powder coat finish. The zinc can be scratched much more easily.
Because zinc behaves in a sacrificial way, reacting with oxygen before the steel, it will slowly deteriorate. Even with a chromate conversion slowing down the outer skin reaction, eventually the zinc will be eaten up. This is highly dependent on the environment the parts are in. This process could take years, or even decades fairly easily under the right conditions.
Again, because of the fact that zinc easily reacts with the environment, it’s not suited for marine or ocean environments where the higher humidity and salt speed up that process.
You can read more about the benefits of plating here.
Pros of Powder Coating for Corrosion Resistance
One big advantage for powder coating is that it is a hard, inert, almost plastic-like shell. That shell seals out the environment that could react with the steel underneath. It doesn’t react with much, making it well suited for applications that might be exposed to certain reactive environments like chemicals, moisture, etc.
In general powder coating provides a very tough, thick surface. It is thicker than most other coatings, including zinc plating. It is often used to coat automotive wheels because it can take a little abuse without much damage.
Cons of Powder Coating for Corrosion Resistance
While powder coat makes a tough sealing shell around the steel, if that shell is damaged, exposing the steel, corrosion will start. Unlike zinc plating, powder coat isn’t able to protect steel once it’s exposed so that corrosion can continue to spread.
Commonly considered an advantage for corrosion resistance, powder coat is fairly thick. This helps its strength and protection, but has the disadvantage of being able to affect how your parts fit together.
Other considerations
In this article we’ve tried to focus on the corrosion resistance benefits of zinc plating and powder coating, but that isn’t the only thing to consider when choosing between these two processes. Here we’ll cover a few other factors you may want to consider when making your choice.
Appearance
Appearance is clearly a personal preference, but there’s no denying the variety of appearances available with powder coating vastly outweigh zinc plating. With zinc plating, it gets its unique appearance during the chromate conversion. Clear, yellow and black are the three options we offer. They do add a colorful appearance, but they aren’t necessarily a uniform consistent color. Zinc plating is also transparent/translucent and you’ll still see the material underneath. This means for bent components you may see bending die marks on each side of the bend. Plated parts are also not deburred, so you could see edge cut marks and any material imperfections through the plating.
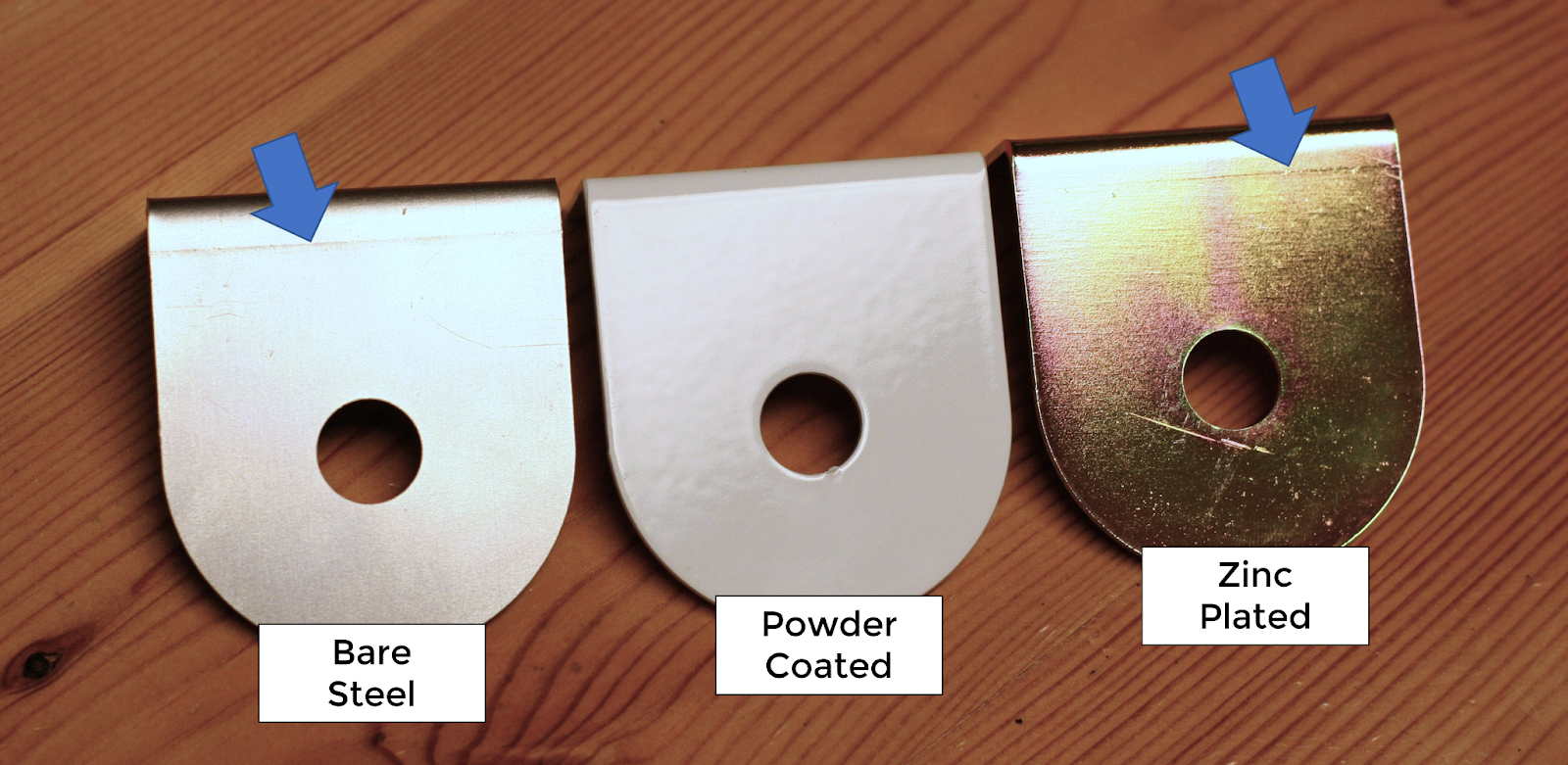
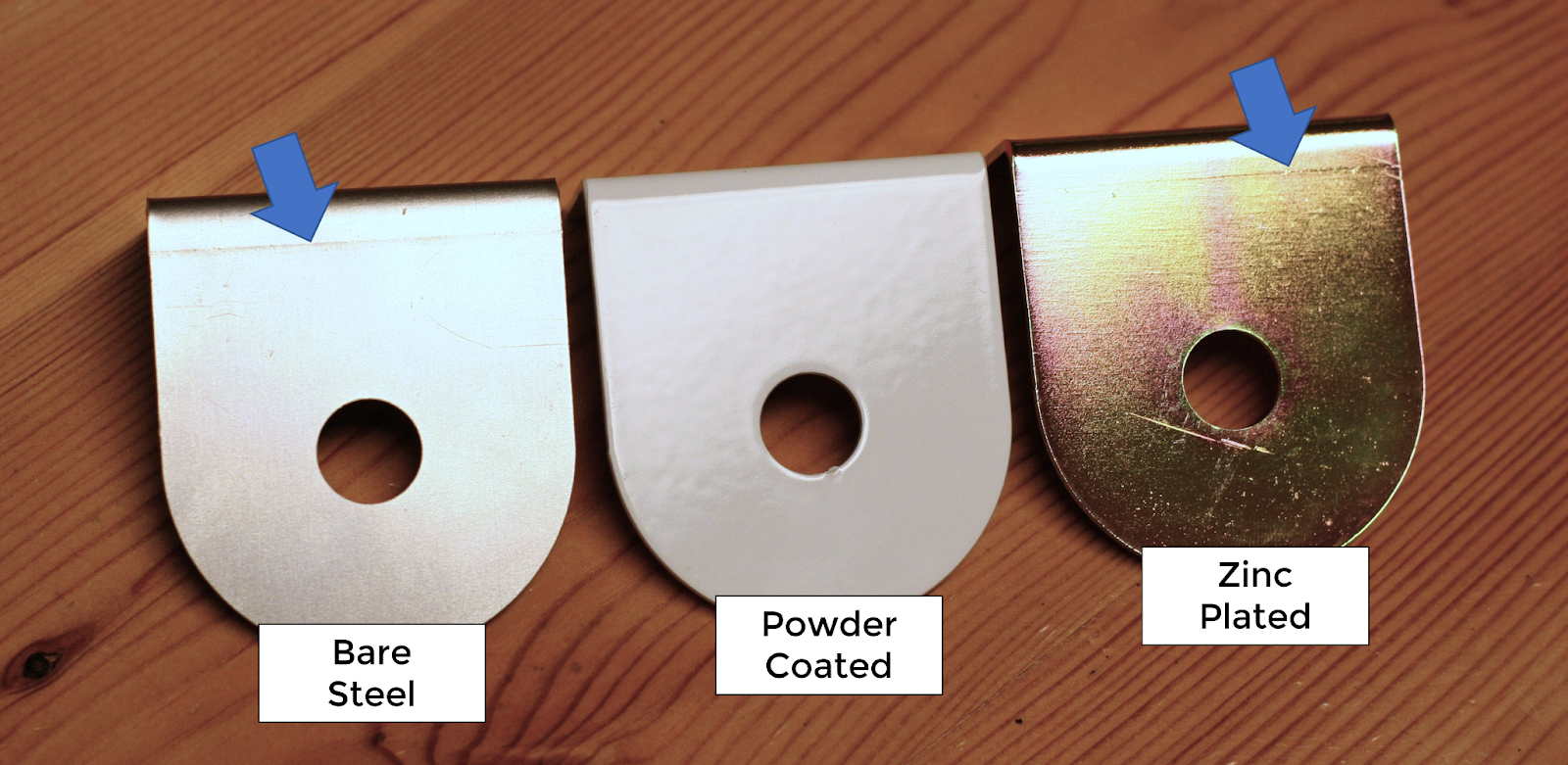
This isn’t true for powder coat. Powder coating is an opaque finish. It’s also a thicker finish and can help to hide minor imperfections in the substrate surface. Powder coat can also be done in a textured surface if your application could benefit from that option.
It is common to use zinc plating on steel parts to get a certain level of corrosion protection and then apply paint or powder coat over top of that to get the desired appearance (and additional protection). Zinc plating is an excellent base for paint or powder, but that does require an additional process. SendCutSend does not currently offer both zinc plating and powder coating on the same part. Although we can powder coat our G30 steel, which is galvanized, another form of zinc protection.
Thickness
Powder coating is a thicker coating than zinc plating. It can be several thousandths of an inch thick. This can be considered an advantage when it comes to protection against corrosion, but may be a disadvantage when fitting parts together. If you powder coat your parts that need to fit tightly together, you’ll want to account for that little bit of extra thickness. You should also consider this thickness when cutting small features into parts that you want powder coated. Take a look at our powder coating guidelines for more specifics.
Zinc plating on the other hand adds almost no thickness to the surface of the part. It’s thin enough that threaded parts can be fully zinc plated without negatively impacting thread fit. Powder coated parts with threaded holes will require the threads cleaned out after you receive your parts. Our press-in hardware, however, is masked prior to powder coating and will not require chasing/removing powder from the threads.
Heat and Electrical Conductivity
Zinc plating will transfer heat more easily than powder coating. Depending on your application, you may want heat to be transferred easily or a more insulating effect.
Similarly, zinc plating will have a higher electrical conductivity than powder coating. It’s good practice to make electrical connections to a bare, uncoated surface, but you can often connect to zinc plating without problems. Powder coating on the other hand can cause issues if it’s between electrical connections. That said, powder coating shouldn’t be used in place of proper electrical insulation if that’s what your project needs.
Which is Best for Your Project?
When it comes to choosing the best method for protecting your laser cut steel parts from corrosion, zinc plating and powder coating are both excellent options. There are a lot of factors you’ll want to consider when making your choice. How will your part be used? Will you need tightly controlled interfaces between your parts? What kind of environment will it be exposed to? How long do you want it to last?
We can’t decide for you, but we can provide a few examples of applications where we might use each method.
Examples
- Parts that will be visible and need to look their best. In this application we’d suggest powder coating. It provides a nicer looking finish.
- Parts that may need to be modified after receiving them from SendCutSend. Sometimes you want your parts to have some protection, but you know you’ll need to custom fit them or modify them in some way after you get them. In that case, zinc plating is probably a better option. The zinc surrounding the exposed steel will still provide some protection.
- Parts that require moving contact with other parts. For something like this we’d suggest zinc plating. Moving contact between parts is likely to damage any finish. Because zinc is a thinner coating than powder coat, it will not impact the fit between components as much. It’s also able to provide protection even after the coating is damaged and the steel is exposed.
- Parts in marine environments. For parts used near the ocean, steel is not a great choice. If you need to use steel in that environment, we’d use powder coating over zinc plating. The salty, moist environment speeds up reactions so the zinc won’t last long. Powder coating is virtually unaffected by salt water, but if it gets damaged and some of the steel is exposed, corrosion will happen quickly.
- Steel parts that need to match the appearance of non-steel parts. In this case you’d have to use powder coating on both the steel and non-steel parts. Zinc plated steel is a unique look that isn’t going to match a finish on another material. If you want your steel, stainless steel and aluminum parts to match, choose powder coating.
Conclusion
To wrap up everything we’ve covered here, both powder coating and zinc plating are excellent finish options that provide a great level of protection against corrosion. Powder coating is available in a variety of appearances and leaves your parts with a tough polymer shell that can stand up to some abuse. Zinc plating, while not nearly as durable or available in as many colors as powder coat, has the unique ability to protect the steel substrate even if the coating is damaged.
There are a lot of things you’ll want to consider and we hope the information provided here helps you to decide which finish is best for your project. If you want any additional information on zinc plating or powder coating (or any of the services we offer), our blog is full of great articles on both of these processes. For some inspiration or just to see what kinds of parts can be made with laser cutting, powder coating and zinc plating, check out the Customer Showcase.
Related Articles From the Blog:
Paint or Powder Coat? That is the Question
How to Optimize Parts for Powder Coating
Top 6 Materials for Powder Coating
6 Tests Show the Durability of Powder Coating
Guidelines for Sheet Metal Plating
Plating
The Benefits of Zinc Plating in Laser Cutting